Как-то один мой знакомый Дмитрий, директор среднего по размерам многопрофильного холдинга, попросил высказать мнение о процессах. Его интересовало насколько оправдано применение процессов в бизнесе.
Свой ответ я, было, начал с традиционной теоретической базы. Мол, это современный подход, он позволяет наиболее рационально направить ресурсы на получение продукта, их описание, как в базе данных, так и на бумаге, помогает лучше понять и оптимизировать бизнес и т.д. Однако в тот момент вспомнил довольно яркий образ, как выглядят процессы в реальности.
Однажды по делам своей практики был на свежепостроенном автозаводе Фольксваген групп в Калуге. По случаю мне организовали экскурсию по его цехам. Там-то мне и довелось наблюдать процессы вживую.

Конвейерный хребет то причудливо извивался на уровне первого этажа, то стремительно поднимался на второй, а порой и вовсе терялся над перекрытиями и незаметно перетекал в соседний цех. Сложно поверить, что лишь сто лет назад конвейер был впервые применен Фордом для производства единым потоком.
Процессы – это небольшие ручьи и реки, берущие начала от какого-то события и завершающиеся озерами и морями, куда они несут свои результаты. При этом на стабильность результата, т.е. продукта, который нужен потребителю, влияет точность выполнения всех операций в процессе. Помните знаменитое «Кто пришивал пуговицы?» Райкина? Стандартизованные и стабильно выполняемые процессы – хороший способ получать продукт с заранее заданными свойствами. На этих принципах построены все системы качества: стандарты серии ИСО9000, Six Sigma, Lean Manufacturing, и т.д. Именно оптимально спроектированные и верно выстроенные процессы позволяют получать продукты, которые согласно стратегии приведут к намеченным долгосрочным целям.
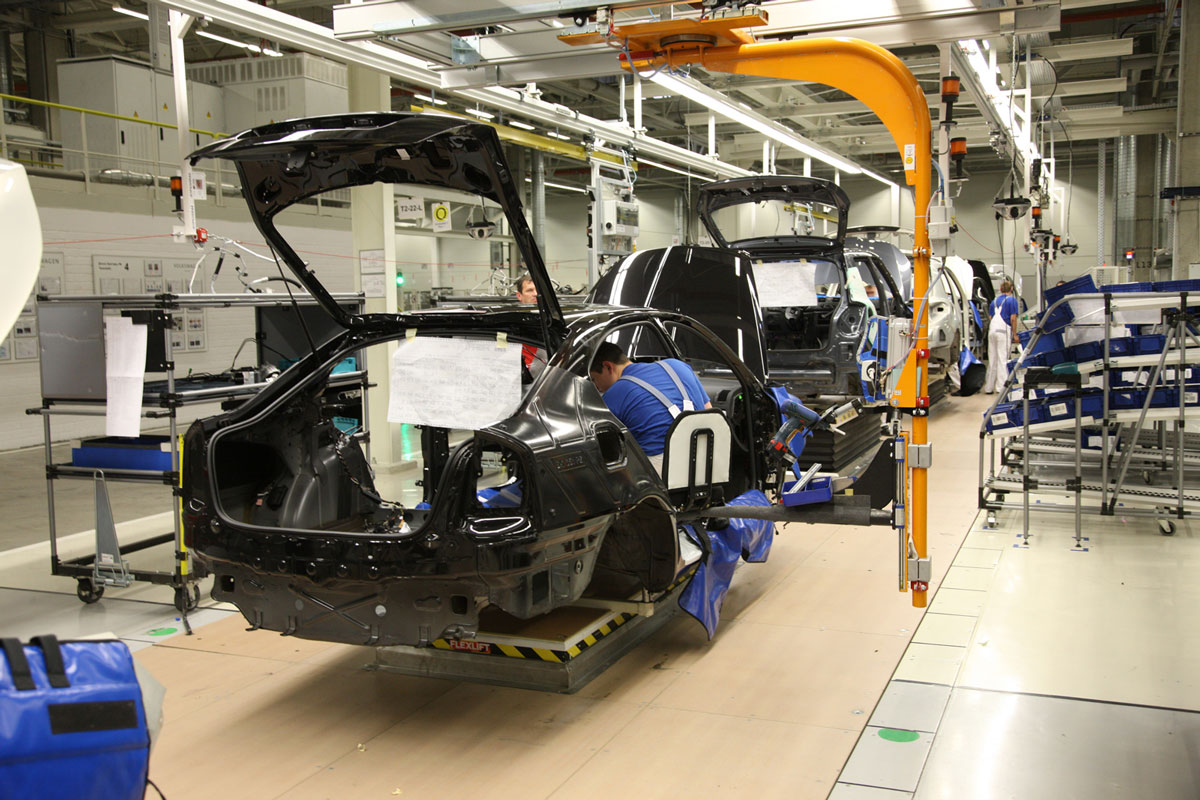
Стандартную цеховую площадку под выбракованные автомобили на российском Фольксвагене пришлось несколько расширить, перенеся вспомогательные помещения. С одной стороны, это говорит о несколько худшем качестве работы новенького конвейера (надеюсь, что лишь пока, т.к. загружен он лишь примерно на 5% – отладка), с другой – о мощной и действенной системе контроля качества. Иначе все машины с недостатками были бы просто навязаны дилерам и проданы. В пользу контроля качества говорит почти анекдотичный случай, когда порядка полторы сотни разноцветных Тигуанов вернули на завод с площадки готовой продукции из-за дефектов покраски, обязав ездить на них средний менеджмент (которым по должности полагался автомобиль). По замыслу немцев это ежедневно должно вызывать чувство неловкости за брак, способствовать большему рвению и побуждать радеть за качество.
Многие компании традиционно группируют процессы по организационному признаку. Это лишает их гибкости и сильно усложняет
- Связь со стратегией, т.е. долгосрочное существование бизнеса
- Их выполнение, т.е. согласованность с другими процессами
- Регламентацию, т.е. стабильность и качество
C некоторой долей иронии можно попробовать представить работу конвейера на основе организационных подразделений: вот в уголочке расположился служба комплектации покрышек с отделами по летней и зимней резины; вдоль стеночки раскинулось управление по пластмассовым деталям, а прямо в центре цеха – департамент металлических комплектующих.
Впрочем, ирония запросто может перейти в сарказм, если вспомнить, сколько компаний организовано на основе подразделений. Страшно представить, чтобы произошло, начни разные отделы, департаменты и управления на конвейере бороться за свою важность в компании, выпячивая свою статусность.
Уникальность не в причудливости процесса, а в его понятности и некоторых особенностях, в том числе технологических, отдельных его частей. Например, на том же Фольксвагене есть примеры уникальных частей выполнения процессов. Однако никому не приходит в голову выделять их из общего ряда работ, выполняемых на конвейере, и как-то дополнительно поощрять. Более того, эти операции полностью автоматизированы.
Наверное, самая удивительная полностью механизированная операция на заводе – сопряжение кузова и собранной в единое целое подвески. На местном сленге это называется «женить». Представьте сколько точек необходимо совместить на двух собранных немного ранее конструкциях, и вы проникнетесь сложностью инженерного решения. Добавлю, что «женят» все собираемые на заводе автомобили – и паркетники, и легковые, как Фольксваген, так и Шкода, – на едином устройстве, а конвейер подает разные корпуса поочередно. Т.е. только что «поженили» Тигуан, следом идет Октавия и т.д. И все это без вмешательства человека.
Еще одна уникальная операция состоит в лазерной сварке крыши автомобиля с боковинами кузова. Если обращали внимание, на продукции Фольксваген групп (Ауди, Фольксваген, Шкода) нет резиновых продольных полос на крыше, которыми прикрывают места контактной сварки на всех остальных автозаводах. Установка лазерной сварки делает единый ровный шов, не подверженный коррозии и более надежно скрепляющий элементы корпуса. Эта установка уникальна, сделана по заказу, довольно дорогостояща в эксплуатации – из 50 кВт потребляемой энергии лишь около четырех идет на саму сварку, остальное – охлаждение, вентиляция и механическое обеспечение, т.к. операция производиться в закрытом боксе без участия человека. Наблюдать за операцией можно через специальные ТВ-мониторы.
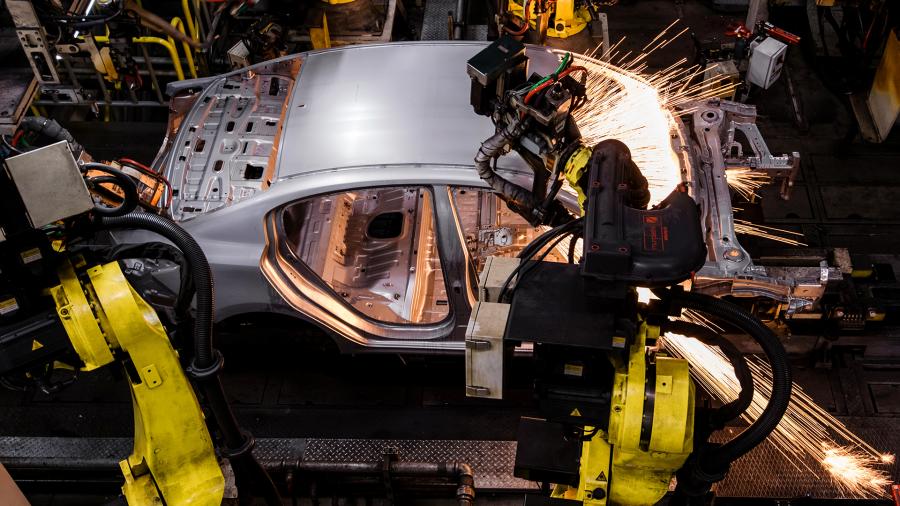
Добавление на каждом этапе ценности в конечный продукт – основа построения процессов. Все остальные функции лишь обременяют продукт дополнительными затратами и, как следствие, ведут к упущенной прибыли или, в отдельных случаях, потере конкурентного преимущества.
Выстраивать процессы не только можно, но и весьма полезно для бизнеса. По сути, это единственный способ организовать сложный бизнес, в котором множество направлений с многочисленными продуктами. Это путь ориентации бизнеса на потребителя, который выбирая продукт (или услугу), будет своими деньгами оценивать качество результата и способствовать росту бизнеса. Нужно лишь быть осторожнее с их автоматизацией, т.к. вещь эта затратная, и не всегда хорошо получающаяся.
Вспоминая посещение завода Фольксваген, порой испытываю удивление от того, как за несколько лет в чистом поле построен завод полного цикла. И практически сразу начал выпускать качественные немецкие автомобили. Перемещаясь по цехам, довелось наблюдать осмысленный и слегка обеспокоенный взгляд нечастых рабочих, что дает надежду на успешность этого проекта.
P.S. Отдельное и большое спасибо Михаилу, который провел по цехам и со знанием тонкостей показал (и подробно рассказал!) об особенностях производства.
Добавить комментарий